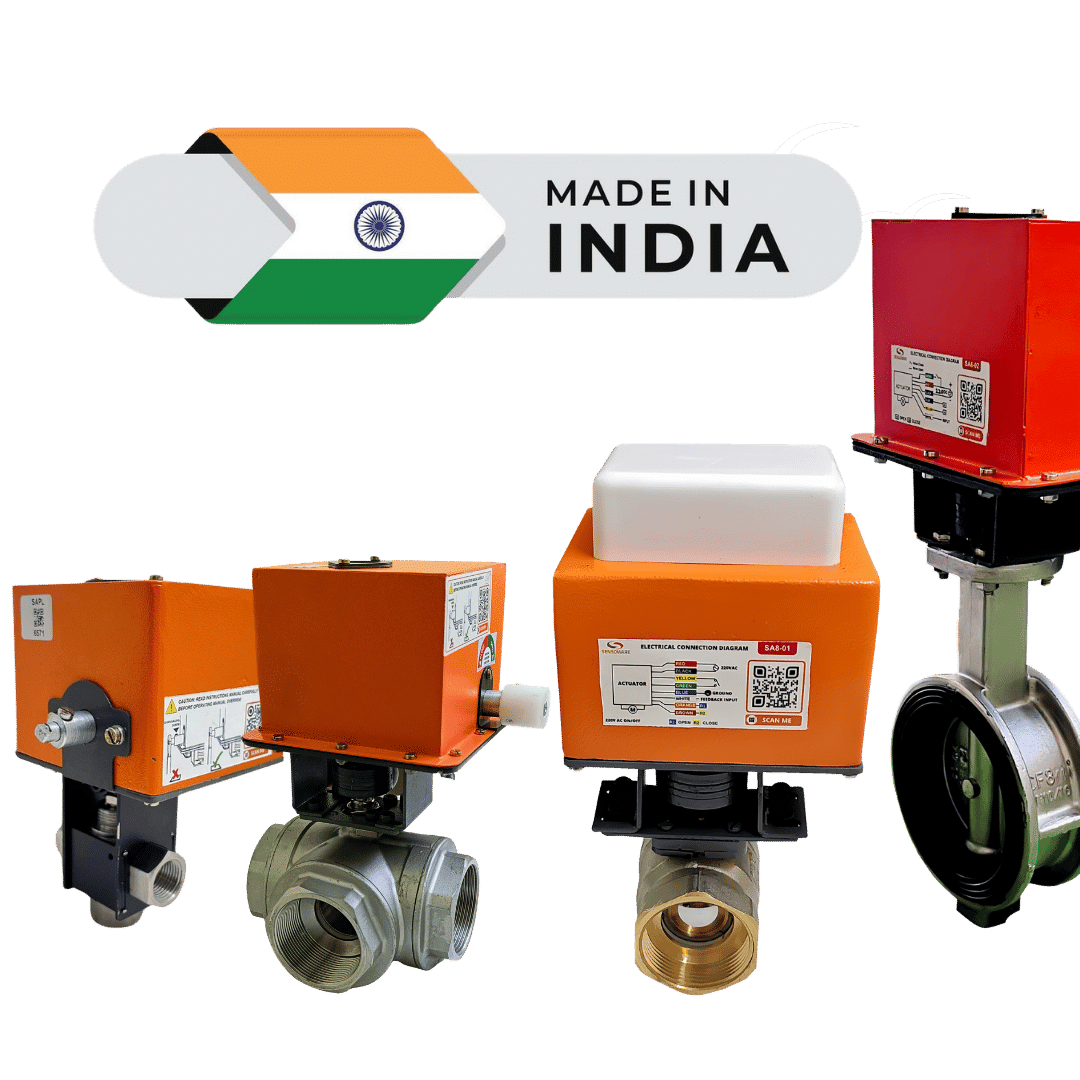
Manufacturer of Motorized Valves and Actuators
We are a Manufacturer, Supplier, and Exporter of Motorized Valves (Motorised Valves) and Valve actuator based in Chennai, Tamil Nadu, India.
Sensoware Offers Various types and sizes of Valves, such as Butterfly, Ball, Sluice, Globe, and dampers with Electrical Actuators. Learn more about our Motorized Valve and Electric Actuator that are available in quarter-turn and Multi-Turn types with ON/OFF or Modulating Functions.
What is a motorized valve?
A Motorized Valve, also known as an electrically actuated valve, is a type of valve that is operated electrically or electronically via a motor. It allows for remote or automated fluid flow control in a pipeline or system. Motorized valves are commonly used in HVAC systems, water treatment plants, industrial processes, and other applications where precise control over fluid flow is necessary.
What is the purpose of a motor operated valve?
The primary purpose of a motor operated valve (MOV) is to automate the control of fluid flow in various industrial processes and systems. MOVs enable remote operation and precise control over the flow of liquids or gases by using an electric motor to actuate the valve. This automation improves efficiency, reduces manual labour, enhances safety by enabling quick response to emergency situations, and allows integration with control systems for better overall process management.
The purpose of an electric motor valve is to provide automated and precise control of fluid flow in a system, allowing for remote operation and integration into automated processes.
When to use a motorized valve?
Motorized valves are best used when automated, remote, or precise fluid flow control is required. They are ideal in HVAC systems for zone control, water treatment plants for process automation, industrial applications for operational efficiency, and fire protection systems for emergency response. Their versatility and ability to integrate with control systems make them suitable for critical and hard-to-access locations where manual operation is impractical.
Use Sensoware automated valves for precise, remote, and reliable fluid flow control in systems requiring efficient and accurate operation.
How to operate a motorized valve?
Operating a motorized valve involves understanding its control system and the specific application requirements. First, ensure the power supply and control signal connections are properly made according to the manufacturer’s instructions. Typically, the valve will have a manual override, an actuator, and a control unit. Use the control unit or remote interface to send commands for opening or closing the valve. The actuator will receive these commands and move the valve to the desired position. Monitoring systems, such as position indicators or feedback signals, can help confirm the valve’s status. Always follow safety protocols and maintenance guidelines to ensure smooth operation.
A servo-controlled valve uses a feedback system to precisely regulate fluid flow and maintain accurate control in response to changing conditions.
Advantages of Electric Actuator for Valves
Electrical actuators for valves or Motorized Valves offer several advantages that make them an attractive choice in various applications.
Precision and Control
Electrical actuators provide precise control over valve position, allowing for fine adjustments and accurate flow regulation.
They can be easily integrated with control systems for automated operation, ensuring consistent and repeatable performance.
Energy Efficiency
They consume energy only when adjusting the valve position, unlike pneumatic or hydraulic actuators, which may require continuous energy supply for maintaining positions.
This can lead to significant energy savings over time.
Low Maintenance
Electrical actuators typically have fewer moving parts compared to pneumatic and hydraulic actuators, resulting in lower wear and tear.
They do not require regular maintenance like lubrication or replacement of seals and filters.
Environmentally Friendly
They do not rely on oil or air supply, eliminating the risk of leaks or contamination. This makes them suitable for applications where cleanliness is critical, such as in food and beverage, pharmaceutical, and semiconductor industries.
Ease of Installation
Electrical actuators are generally easier to install since they do not require complex plumbing or tubing.
They can be directly connected to the power supply and control system
Versatility
They are available in various sizes and configurations.
Electrical actuators can be used in diverse applications, including HVAC, water treatment, industrial automation, and more.
Integration with Smart Systems
Modern electrical actuators can be equipped with advanced features such as diagnostics, feedback, and communication capabilities. They can integrate with IoT and Industry 4.0 systems for enhanced monitoring and control
Safety
Electrical actuators can be designed with fail-safe features to ensure that valves move to a safe position in case of power failure.
They can also include overload protection to prevent damage to the actuator and valve.
Cost-Effective
While the initial cost might be higher than pneumatic or hydraulic actuators, the overall lifecycle cost is often lower due to reduced maintenance, energy savings, and longer service life.
motorized ball valves
Ball valves with electric actuators are widely used in various industries for automated fluid flow control. They allow for remote operation and integration into automated control systems, minimizing the need for manual operation and monitoring.
2 Way Ball Valves with electric actuator
Available in wide range of material options to choose from, PVC, UPVC, CPVC, Brass, SS304, SS316 Stainless Steel, PTFE, Polypropylene etc.
Wide range for Ball Valves with Electric Actuators
General Technical Specifications
Material | PVC, UPVC, CPVC, Brass, Stainless Steel SS304 / SS316, Polypropylene PP, PTFE |
Size Range | 1/4 inch to 10 inch |
End Connection | Socket End, Screwed End, Flanged End Class 150, Tri Clover / Tri Clamp Ends. |
Number of Ports | 2 Way, 3 Way, 4 Way |
Port Configuration | L Port, T Port, LL Port or X Port |
Seat | PTFE, EPDM |
Temperature Range | 0° to 220° C |
Pressure Range | 3 Bar to Class #900 |
Actuator Type | Electric Actuator / Motor Operated |
Function | ON/OFF, Floating, Modulating 4-20mA or 0-10V DC |
Travel Angle | 90°, 180°, 360° |
Operating Speed | 2 Seconds to 90 Seconds |
Voltage Options | 5V DC, 12V DC, 24V AC/DC, 220V DC, 220V AC, 415V AC |
Feedback Output | Voltage Output, Potential Free Output, Analog Signal 4-20mA or 0-10V DC |
Manual Override | Optional |
Ingress Protection | IP 54 to IP 67 |
Confused on choosing the product you need?
Don’t worry. We are there to help you with the right product based on your requirements.
Motorized Butterfly Valves
Motorized butterfly valves are widely used in various industries to control the flow of fluids. They consist of a circular disc mounted on a rotating shaft, and when the valve is fully closed, the disc blocks the flow of fluid. When the valve is fully open, the disc is rotated a quarter turn, allowing fluid to pass through.
General Technical Specifications
Material | UPVC, CPVC, Brass, Stainless Steel SS304, Polypropylene PP |
Size Range | 1.5 inch to 12 inch |
End Connection | Wafer End, Lug type, Flanged End Class 150, Tri Clover / Tri Clamp Ends. |
Types of Butterfly Valve | Zero Offset Butterfly Valves. Double Offset Butterfly Valves. Triple offset butterfly valves |
Port Configuration | L Port, T Port, LL Port or X Port |
Seat | PTFE, EPDM |
Temperature Range | 0° to 150° C |
Pressure Range | PN10, PN16, Class #150 |
Actuator Type | Electric Actuator / Motor Operated |
Function | ON/OFF, Floating, Modulating 4-20mA or 0-10V DC |
Travel Angle | 90°, 180°, 360° |
Operating Speed | 2 Seconds to 90 Seconds |
Voltage Options | 5V DC, 12V DC, 24V AC/DC, 220V DC, 220V AC, 415V AC |
Feedback Output | Voltage Output, Potential Free Output, Analog Signal 4-20mA or 0-10V DC |
Manual Override | Optional |
Ingress Protection | IP 54 to IP 67 |
Ball Valve or Butterfly Valve. Which one to Choose?
Operate the Valve the way you want it.
We have three types of operating methods for all our range of Motorized Valves and Electric Actuators.
ON or OFF
This type of valve uses an electric motor to open or close the valve fully, rather than adjusting it to a partial position.
Floating Type
When you wanted to inch between open and close. There can be many points at which the actuator can be stopped.
Modulating Control
Electric Control Valve to control the flow rate of a fluid by continuously adjusting its position between fully open and fully closed using 4-20mA.
Presenting 3-Way and 4-Way Electric Actuated Ball Valves
Three-way and four-way electric ball valves are specialized types of motorized valves used to control the flow of fluids in more complex piping systems. These valves can direct fluid flow through different pathways and are commonly used in heating, cooling, and process control applications.
Frequently Asked Questions
Here’s why Industrial Automation Companies
Sensoware
Follow our Social Channels